The Australian Federal Government has committed A$25 billion to the development of the country’s renewable energy resources. This investment has unleashed a tidal wave of corporations bidding on these projects, all lobbying to be at the forefront of Australia’s renewable energy industry development. In New South Wales, the creation of five Renewable Energy Zones to power the state as they transition away from coal-fired power has created a wave of new wind and solar projects. But in the rush, many of the companies pitching to develop these projects have passed over one key aspect for their success: supply chain management and logistics. These projects take place in remote locations without the supporting, port, lay down, road and logistics related infrastructure and the supporting services and general capability to deliver. Without proper logistical management, these factors can lead to serious challenges for the efficient completion of these vital projects. Here’s how Siecap recommends that Australia’s forefront of renewable energy projects address their logistics and supply chain challenges.
The Logistics Challenges
In our work advising Australia’s core industries on supply chains and logistical structures, we see firsthand the challenges faced when businesses do not include enough logistics and supply chain feasibility assessment in the planning process. Failure to include the supply chain and logistics planning function at the inception of a project is the leading cause of blown-out budgets, failure to meet deadlines, and can even be traced back as the key reason a project fails. Typically, project failures are caused by one of the following reasons:
- Pre-feasibility: A lack of logistics pre-feasibility analysis, leading to insufficient understanding of port, road, lay down and handling capacity, constraints and costs and a lack of specifications input for procurement and engineering.
- Disconnect: A disconnect between stakeholder groups such as construction, procurement, and logistics with poor cross-party reporting and communication protocols.
- Traceability: Poor material traceability and quality assurance standards leading to a lack of visibility and control.
- Contract Compliance: Third Party logistics providers not always acting in the best interest of the project with contract compliance insufficiently managed.
- Statutory Requirements: Poor appreciation for country of origin and country of delivery logistics constraints and statutory and approval requirements.
- Tariff Management and Terms: The suboptimal set up of tariff management, duty minimisation and Incoterms.
The Problem
Projects of any kind – but particularly infrastructure projects – cannot begin without materials. This means that the majority of businesses focus entirely on having those materials, rather than the costs of doing so. This trend is driven by a lack of understanding, risk aversion, a lack of tracking systems, and complicated supply chains, with a variety of parties involved in both the operation of existing assets and the execution of capital projects – and little coordination or planning between them.
Making materials available and understanding the logistics envelope for managing materials for projects and production sites is obviously vital, as the costs of a missed day of production or delay in the project commissioning date are significant. But with effective logistics planning there are opportunities to reduce the costs of running the assets or executing capital projects without compromising materials availability.
Some examples of project failures resulting from poor logistics planning that have been identified by Siecap include:
- Little or no coordination, planning and staging of materials acquisition and delivery to sites. This impacts the coordination of resources on site (eg. installers, cranes, etc) resulting in construction delays and cost overruns, and can impact Chain of Responsibility and fatigue management obligations.
- Failure to plan for the movement of prefabricated modular equipment to sites where route limitations have resulted in significant delivery delays, requirements for unplanned equipment modifications, and additional costs for support resources (eg. to lift power lines).
- Lack of transport resources coordination resulting in duplication of requirements and under-utilisation of fleet availability. This can be particularly costly where the project site is relatively remote (and trucks arrive at site half-full).
- Failure to coordinate transport requirements with regulatory authorities delaying approval processes (police, local Government, State Departments, etc).
- Loss of potential savings, such as customs import concessions and EPBS tariff exemptions, due to the failure to correctly identify equipment origins or to complete required preliminary documentation.
- A blow out in tariffs and duty charges owing to incorrect import concession assumptions being budgeted without appropriate research or knowledge of legislative changes.
- Lack of coordination of imported equipment and related delivery requirements resulting in poor delivery visibility, delivery planning delays and cost increases (as well as unbudgeted storage and import duty costs).
- Poor materials and services contract specifications and award processes resulting in poor contractor support, limited supplier performance management opportunities, and increased costs as a result of contract ‘variations’ when oversights are identified and remedied.
When not considering the threats above, businesses inhibit optimal project performance and see increased risk exposure, schedule delays and cost blow outs that could be mitigated through early stage logistics planning.
It’s Never Too Late
Even when a project is already deep into implementation and rollout, a supply chain and logistics expert review will be a vital asset. While having someone onboard from the earliest pre-feasibility planning processes is the best strategy to deliver the ideal outcomes, late is still better than never.
In cases where a project has already commenced, employing the logistics and supply chain capabilities necessary to undertake a detailed logistics audit to ascertain how well logistics requirements have been addressed to the current point of the project rollout phase, and to make recommendations of opportunities for improvement, is highly recommended in order to identify potential issues, establish benchmarks, and provide a baseline for implementing improvements.
The diagram below shows a typical logistics audit process that focuses on ensuring that all project logistics support requirements are being optimised, highlighting opportunities for improvement.
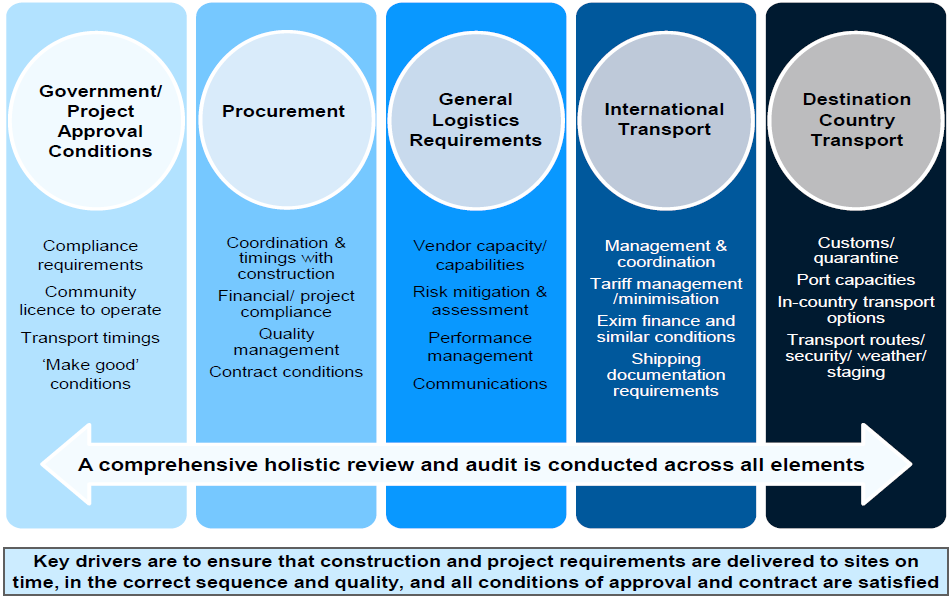
The Benefits of Logistics Planning
An effective project logistics planning strategy will drive significant cost savings and process improvement benefits.
These include:
- Empowering choice. Developing strategies and executable tactical options to reduce costs, improve schedules and minimise risk.
- Optimisation of total costs. Maximising modularisation envelopes and optimising total cost between on-site labour, engineering and logistics.
- Risk mitigation and constraint exploitation. Identifying areas of risks from operational, safety, community, approval or corporate reputation perspectives and developing appropriate and sustainable mitigation strategies.
- Resource and schedule optimisation. Understanding the key cost and value drivers to enable optimised service options to improve performance, cost and schedules.
- Assurance of compliance. Ensuring conditional approval and regulatory requirements are identified, documented and captured through logistics execution plans and operational auditing.
- Transport costs. Reduced project transport costs by up to 20%.
- Work flows. Stabilised construction equipment and operations requirements work flows.
- Project support. Improved levels of project support and service levels.
- Contractor compliance. Improved contractor compliance with conditions of project approval.
- Delivery lead times. Reduced delivery lead times with more delivery predictability and control. This also supports improved freight optimisation and transport flow/coordination.
- Project risks. Improved project risk understanding and assessment, and improved risk management.
The Next Steps
To reduce industry costs, prevent failures, and help expedite the advancement of Australia’s push towards a renewable energy grid, logistical planning must be made a core aspect of planning processes. For a business – and the industry at large – to be successful in these projects, logistics must be given a seat at the table from day one.
The keys to logistical success are:
- Early Planning. Commence planning as early as is possible to ensure there is a clear understanding of key risks and responsibilities, and suitable mitigation strategies are developed.
- Phased logistics implementation plan. Development of a detailed logistics plan to support the project through each phase. The logistics plan will support investment decisions and sound financial analysis, as well as supporting social, environmental and sustainable development analysis.
- Front End Loading. Initiate early analysis of key phases of the project to identify capacity and constraints along the value chain and key logistics support requirements, and review the effectiveness of the completed processes before moving to next and subsequent phases.
- Determine a contracting strategy. The contracting strategy should be determined early in the project evaluation process, which should include a sound risk management approach.
Siecap has been adding value to major organisations in Australia and internationally
in the provision of advice and support for identifying how logistics for capital projects and operations can be improved, how project costs can be stabilised or reduced, and project time frame compliance strengthened. If your project has seen logistical challenges causing financial and timeline pressures, Siecap’s logistics and supply chain experts can be engaged quickly to help you understand and overcome these threats to project completion.
Please contact us any time to arrange a no obligations meeting and understand how Siecap can add value to your organisation’s logistics and supply chain processes.