Inventory Location Management
A JOURNEY TO ACHIEVE WAREHOUSE INVENTORY CONTROL & TRACKING
SUMMARY
A readymade meal and snack company was embarking upon its third decade of Melbourne based manufacturing. Currently operating out of two high capability warehouse facilities that entailed the use of chilled, frozen and ambient storage. They have at any one time around 1,000 pallets of inventory on hand.
The client was struggling with poor inventory tracking and engaged Siecap to work through the issues and assist them in identifying the right solution to support the business’ next wave of expansion.
OVERVIEW
Due to a growth and its resultant pressure on storage space, human error in picks and packs resulted in misplaced raw and finished inventory pallets that are held across their two manufacturing facilities. This was chiefly due to an absence of tracking solutions, like rack labelling and the necessary infrastructure of a digitally effective inventory management system, for reliable inventory counts, recording, tracking raw materials and finished goods and providing inventory reports. The direct consequence of ‘losing’ pallets was product waste in the region of a six figure sum per annum.
OUR APPROACH
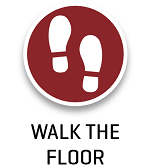
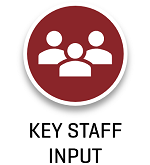
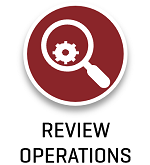
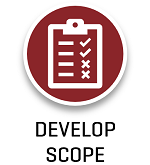
DEFINED NEED
By walking the floor and interviewing key warehouse personnel, an operational systems review of the two manufacturing sites was compiled. From which a scope of operational needs was framed.
None of which was a particular onerous requirement but compared to the existing work practice of ‘from memory’ represented a revolutionary approach to warehouse operations.
THE CHALLENGE
Exacerbating the problem was that the company’s Enterprise Resource Planning (ERP) SAP Business One had not been implemented with the inventory control module turned on.
Meaning that even if basic requirements such as rack labelling was introduced there was no mechanism to use the captured inventory records.
SAP Business One is much stronger at accounting than warehouse management.
Like many businesses embarking on the next cycle of growth, the challenge was the inevitable decision relating to expenditure trade-offs.
STICKER SHOCK
The market is full of warehouse inventory management software solution vendors, making it a crowded place.
Aligning the need to the options out there, is challenging for small / medium enterprises. Especially as initial pricing enquiries can quickly lead to sticker shock, as even the express install of the main WMS providers starts from $45,000 and can quickly escalate to near $100,000.
This shock typically sees the immediate cancellation of the program by many small to medium organisations.
Initially this too proved to be the case for our project team. But knowing that expenditure at this level would be unlikely to be approved the team kept searching.
THE DECISION
Painful as the problem is, overinvesting in the wrong scale of solution would limit the ability to invest in further facility production line upgrades.
Additionally, and typical of small expanding organisations the depth of resources to scope and support system implementations is not substantial, which pointed towards finding a right size solution that could be efficiently and speedily introduced.
In this case an inventory system that had to pay for itself with 12 months was a necessary project goal.
Realising that there should be a better way to operate, they sought help from Siecap to confirm the problem and then work with the warehouse management software industry to find an affordable solution.
LESSONS LEARNED
Your SAP B1 implementation partner may not have the right WMS solution or even understand that you have a need for a WMS.
That’s OK, they are great at financial system set ups and support but perhaps less capable when it comes to supply chain inventory system needs.
Again, that’s OK, as under third line enforcing rules you are not compelled to use their software solutions and you are able to look elsewhere.

FIT FOR PURPOSE
By engaging with three of the six Australian based SAP B1 implementation partners, a ‘fit for purpose’ solution was found in the form of the Produmex Scan platform.
Providing a combination of;
- ease of install via SAP B1 pre-existing connectors,
- low user licensing costs,
- use of existing SAP functionality,
Appealing to clients who only have a limited need for WMS functionality.
Importantly, should Produmex be procured it also comes with a structured pathway to a full-scale WMS through its modular install approach.
- Effective inventory tracking across multiple warehouses,
- Locating pallets to rack locations and quantities to pallets,
- Stock level recording and transfers across facilities,
- Tracking mixed pallets with multiple expiry dates.
- For smaller suppliers being able to generate produce barcodes so receipts could be location controlled
- PO Receipt management, Putaway, Bin transfer, Picks and Packs, Despatch, Lot / expiry date tracking,
- Mobile data capture (RF or return to base PDA
- Print on demand pallet labelling
CONCLUSION
As SAP B1 clients grow in scale, the requirement for implementing base level warehouse management systems functionality will eventually arise. Since the platform is not noted for having a strong supply chain / distribution capability, an examination of add on solutions will apply. Knowing what is ‘fit for purpose’ and meets your budget is a surmountable problem.
Is there benefit to installing a Warehouse Management System (WMS) ahead of other programs?
In our view the answer is yes, because if nothing else you will have one fewer problem to deal with once you know where each pallet of stock now resides in your growing warehouse operation.
Even if the long-term outcome (3-5 years) entails installing a full-scale WMS, the learnings and ‘know-how’ developed through taking the first steps, will put you in good stead to achieve the best inventory system design and deployment.